Modular construction permitting involves two tracks: (1) building large elements of the building in a manufacturing plant away from the project site, and then (2) delivering the buildings to a prepared site, where typical construction activities such as clearing, site grading, utility preparations, and foundations are being constructed.
The permitting of site-related activities are handled by the local municipality’s building department and preceded by typical land approval processes of the city or town. The modular components themselves are subject to state regulatory oversight and a permitting process that is wholly independent. Buildings built in a manufacturing plant have concealed elements that would otherwise not be inspected on-site by the local building officials. That is why most states have design review and inspection programs to ensure that all systems built in a manufacturing plant offsite meet code. How these two tracks of permitting interface, and how it’s best to set up the roles and obligations of the parties, particularly the design professional, is the topic of this article.
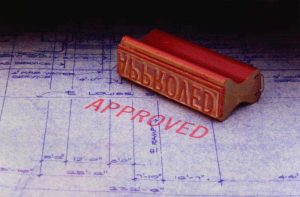
In Massachusetts, our home state, there is a Manufactured Buildings Program. The Program is a part of the Board of Building Regulations and Standards (BBRS) who has authority and governs the design, manufacture, handling, storage, transportation, relocation, and installation of manufactured buildings, manufactured components, and modular homes (See Ninth Edition 780 CRM 110.R3.1.2.). The BBRS is a part of the Department of Public Safety, they ensure that all building construction in the state is safe and meets all code requirements. They work with practitioners in our state to improve our codes in a way that furthers commerce while ensuring safety and quality.
The essence of the Manufactured Buildings Program is to ensure that constructed assemblies built off-site (for any reason ) are inspected prior to leaving the manufacturing plant. The program administration works with private third-party inspection agencies (TPIA’s) who play an important role in making inspections for the state and carrying forth the intent of the program. The TPIA will review design plans stamped by state-licensed professionals showing that all structures and systems are engineered to current codes, and further follow the process through to inspection to ensure the manufacturer builds according to the plans. There is also a labeling requirement. The label is proof to the local official that prefabricated components are built to code.
One question I’m often asked is whether the local architect should contract the factory directly. It is most typical that there is an architect on the project under contract with the Owner or Construction Manager. Most often they play a critical role in early planning and understand all the site-related aspects of the project. Architects will always design buildings to fit the site. In our projects, Triumph Modular is the Construction Manager that coordinates the whole process, most typically with a singular contract with the Owner. In this arrangement, we hire an architect to meet with us and our owner/client to design the modular building. We hire a modular factory as soon as possible to join that team. Our architect stays on with us as the “designer of record” for the purposes of permitting the project locally.
For many years, we did not involve our architect directly in the modular factory state permitting process. It is not a legal requirement to do so. Each modular factory has the responsibility to submit design and engineering plans to the State. They must hire a state-licensed professional to stamp the modular building plans. The factory is licensed by the State and has the legal obligation to arrange inspections and “label” the buildings to complete the process. Every factory understands this obligation clearly. If the proper procedures are not followed, they can lose their license to build in the state.
In a modular project, Triumph always buys the modules from a factory, so there is a purchase agreement between us. In that contractual relationship, the factory recognizes its obligation to comply with the state permitting process when they sell products.
The question that often comes up is whether the factory should also contract with the architect on the project to complete their own fabrication drawings for State review. I’ve spoken to a few industry experts and the answer is not that clear.
One philosophy is to leave the factory to its own devices. There appears to be a conflict of interest if the factory is using the Owner’s (or CM’s) architect for what is a separate scope of work. What if the architect fails to meet a schedule, or fails in some regard in dealing with the TPIA as the factory requires? Will the factory then have an excusable delay in production because the Owner’s architect failed in some regard? If there are late-breaking design changes, our factory will typically send us a proposed change order amount for the amount of expense related to redrawing and re-stamping to receive approval from the state. It is unclear if, as a design-builder, the architect that is overseeing the whole project also needs to bill for change to the modular plans.
The second school of thought is to not worry about the preexisting contract between the CM (Triumph) and the designer (the design-builder). The modular factory should contract with the same design firm, for the following reasons:
- The plans and specs that define expectations for the Owner and detailed for the local permit have already been drawn (to a large degree) so why wouldn’t the same design firm stamp the modular component drawings? Using a single architect ensures that the modular factory helps to build the drawings, and offers design assistance – of critical importance with modular construction.
- Most local and state officials review their documentation with concern for the totality of the building code, particularly when manufactured components are being used. Looking at one package from one design firm is a better approach than looking at two.
Conclusion: all parties to a modular construction project need to understand the inner workings of the State permitting process in order to accurately divide tasks and assign roles and responsibilities.
Hopefully, you have gained an improved knowledge of the two tracks of permitting modular projects (at least in Massachusetts). The “jury” is still out on whether there is a best practice with regard to the above topic, it very well could depend on project size and scope. I hope this article will help you avoid any confusion by officials, which could result in holding up your project.
For the record, my own interpretation of the intent of the program derives from having attended meetings hosted by the BBRS to educate modular practitioners. I’ve also read notices from the TPIA’s to both manufacturers and local officials training them on the program. I have also spent 18 years professionally focused on modular construction projects. Naturally, you should contact the BBRS directly or one of their licensed TPIA’s for further guidance. Also, note that each state is different in how it deals with these issues.
Cost implications of the Program: it is redrawn and rebuilt to the current code. As codes have improved buildings to be more energy-efficient, it is common that older buildings need to have insulation added and lighting improvements. These common types of improvements are good for the building and great for the end-user, they just add some cost.
Schedule Implications: Taking a building through the program takes three to four weeks to get through the drawing approval process, and with some concurrent reconstruction (demo and re-framing prior to inspection) work another few weeks to finish the improvements, have inspections and re-labeling.
We can’t know the exact cost of upgrading to re-label until the updated drawings are approved by a PE and those drawings priced by fit-up crews. We may ask our client to approve the cost of drawings, and we will advise an estimate or allowance for the upgrades being brought about by the program.
Is there an exemption for certain Uses? When for an event or construction use? No. Every multi-section modular building (where 2 or more sections traveling independently need to be stitched together at the site) falls under “The Program.”
In closing, the Massachusetts MFG Buildings program and its application to portable and temporary modular buildings is a very good thing. The program ensures relocatable buildings intended for “coded use groups” (schools, professional offices, etc.) are built by licensed trade people, and all structural, seismic, and other life safety goals of the code are met.